
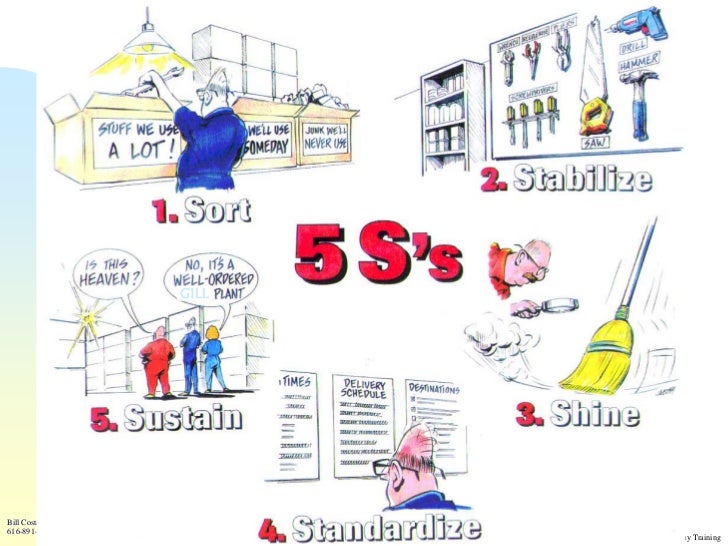
With a just-in-time approach, manufacturers know exactly what and how many parts to stock. This eliminates overproduction, material waste, and inventory storage. Instead of mass-producing cars, Toyota builds based on orders. Just-in-time bases manufacturing on customer demand. This is known as kaizen, a philosophy of continuous improvement that is the foundation of lean manufacturing.Ģ. A balance between machine power and human ingenuity, jidoka allows a manufacturer to fine tune specific steps in their operation as problems arise. Jidoka is the automation of processes that safely come to a halt when an abnormality occurs during production. The Toyota Production System, or TPS, bases its operational approach on two concepts:ġ. This repetition results in continuous improvements in production and quality. Stopping production to fix a part resulted in the ability to both remove a defect before it was completed and to improve a step in the production process. Unhappy with the waste, Toyoda created a flow process where workers stopped and inspected pieces as they moved through their build in order to create a continuous flow. After casting, machining, and building 300 engines, his team quickly realized a defect in the design and had to scrap the batch. In 1934, Kiichiro Toyoda, founder of the Toyota Motor Corporation, decided his company would build its own engines. While the term “lean” came about in the 1980s, the genesis of lean manufacturing happened much earlier. The way to achieve this is to adopt lean manufacturing principles. In order to compete in today’s world and survive the unpredictable nature of the global economy, a company must be agile, able to flex but not break. This is achieved by improving processes, engaging people, and streamlining communication so everyone is aligned and working toward achieving the same goals to increase your company’s value proposition. The ultimate goal of lean manufacturing is to deliver high-quality goods for a lower operating cost.
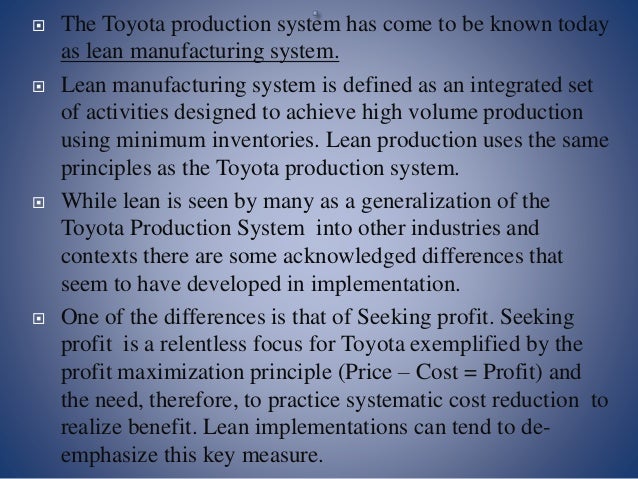
Waste can negatively affect your entire manufacturing operation and can result from: Waste is anything that does not add value and takes away from profit potential. Lean manufacturing is keeping operational elements that add value and eliminating ones that don’t. From people and machines to process and systems, lean manufacturing encompasses every aspect of an operation. Sometimes called lean operations, lean manufacturing is continually assessing and improving the various parts of your organization to reduce waste and keep costs down while boosting productivity, quality, and innovation. But to sum it up, lean manufacturing is operating with minimal waste. If you perform a Google search for a lean manufacturing definition, you’ll find a few different ways it’s explained. But in the age of Industry 4.0, technology has created a prime opportunity for companies to streamline processes, reduce operating overhead, and move into this next industrial revolution with a lean manufacturing approach.ĭiscover top lean manufacturing trends. This concept and practice of lean manufacturing has been around for nearly a century. As markets change and competition escalates, companies are looking for ways to cut costs, boost productivity, and run more efficiently. Lean manufacturing is a growing trend in the industrial world.
